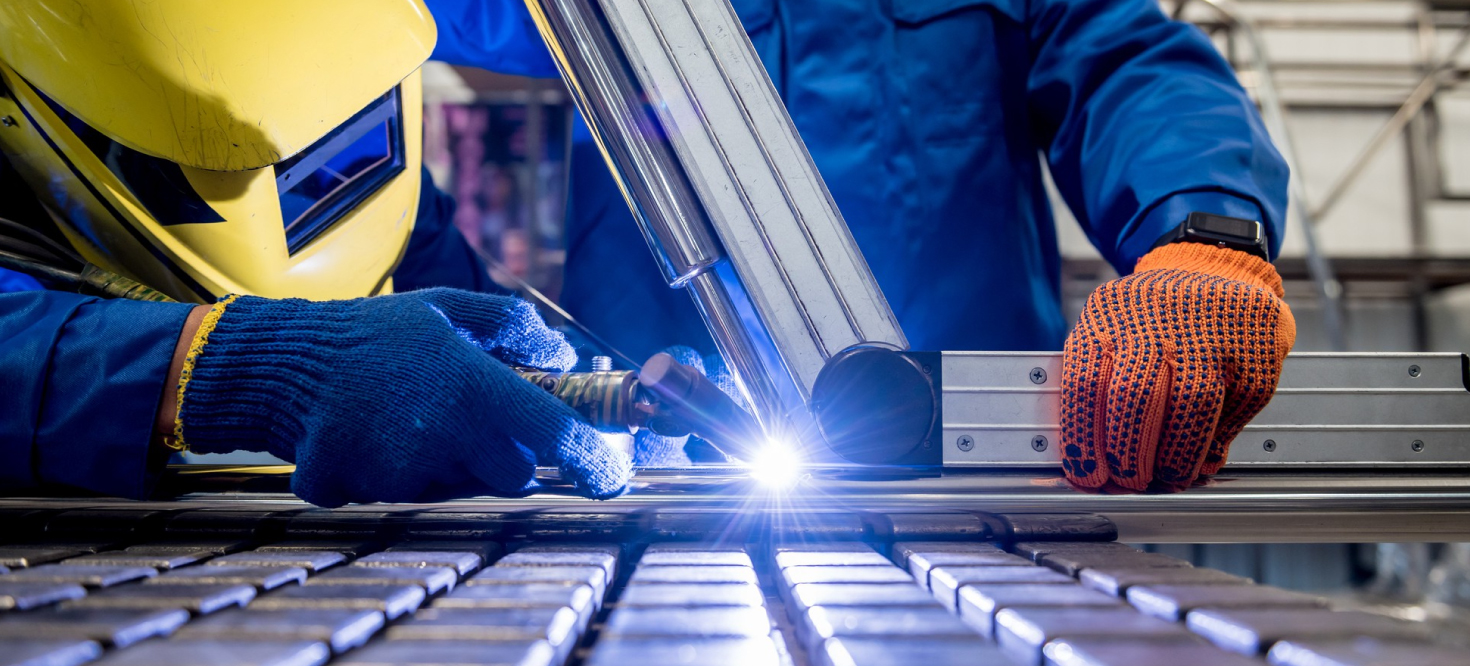
Apr 25 2025
/
A Comprehensive Guide to Aluminum Fabrication Techniques
Introduction
Aluminum’s unique properties, lightweight strength, corrosion resistance, recyclability, and ease of fabrication make it a go-to material in industries ranging from automotive and aerospace to construction and electronics. However, unlocking aluminum’s full potential requires the right fabrication techniques to transform raw material into high-quality, functional products.
Aluminum fabrication encompasses a range of techniques that allow manufacturers to shape, join, and finish aluminum for diverse applications.
This guide covers essential aluminum fabrication techniques, explaining the processes, applications, and benefits of each. Whether you’re interested in cutting, welding, or extrusion, this guide provides a detailed overview of how these techniques contribute to aluminum’s versatility and efficiency in modern manufacturing.
1: Why Aluminum is Ideal for Fabrication
1.1 Lightweight and Strong
Aluminum’s high strength-to-weight ratio makes it ideal for applications where both durability and weight reduction are crucial.
- Reduced Transportation Costs: Aluminum’s lightweight nature makes it easy to handle and transport, lowering logistics costs.
- Enhanced Performance: In applications like automotive and aerospace, aluminum’s lightweight strength supports efficiency, fuel savings, and better performance.
- Extended Component Lifespan: Aluminum’s strength enables it to endure wear and tear in heavy-duty applications, reducing maintenance needs and extending component lifespan.
1.2 Corrosion Resistance for Durability
Aluminum naturally resists corrosion, which is essential in outdoor and industrial applications.
- Low Maintenance Requirements: Corrosion resistance reduces the need for frequent repairs, leading to cost savings and extended durability.
- Suitability for Harsh Environments: Aluminum performs well in humid, salty, and chemically exposed environments, ideal for marine, outdoor, and industrial settings.
- Sustainable Longevity: Aluminum’s durability supports long-lasting applications, reducing waste and supporting sustainable manufacturing.
1.3 Recyclability and Sustainability
Aluminum is fully recyclable, making it a sustainable choice for environmentally conscious manufacturers.
- Energy-Efficient Production: Recycling aluminum uses 95% less energy than producing new aluminum, contributing to lower emissions and environmental impact.
- Support for Circular Economy: Aluminum’s recyclability supports a closed-loop production cycle, where materials are reused, reducing the need for raw resource extraction.
- Alignment with Green Initiatives: Many industries are prioritizing sustainability, and aluminum’s recyclability helps manufacturers meet eco-friendly standards.
These properties make aluminum an ideal material for fabrication, offering adaptability, durability, and sustainability across diverse applications.
2: Cutting Techniques in Aluminum Fabrication
Cutting is the first step in transforming raw aluminum into a workable shape. Different cutting methods provide flexibility, precision, and speed, making them essential for aluminum fabrication.
2.1 Shearing
Shearing is a common mechanical cutting technique that uses a shear blade to slice aluminum sheets without melting or burning.
- Ideal for Sheet Metal: Shearing is well-suited for cutting aluminum sheets and plates, providing clean, precise cuts without heat-affected zones.
- Fast and Cost-Effective: Shearing offers quick processing times, making it a cost-effective option for high-volume aluminum fabrication.
- Minimal Material Waste: This method produces minimal waste, supporting sustainable manufacturing practices.
2.2 Laser Cutting
Laser cutting uses a focused laser beam to cut aluminum with high precision and speed, ideal for intricate designs.
- Precision for Complex Shapes: Laser cutting enables detailed, intricate cuts that are essential in electronics, signage, and decorative applications.
- Minimal Heat Distortion: Laser technology minimizes heat distortion, ensuring that aluminum retains its properties and dimensions.
- Cost-Effective for Small Batches: Laser cutting is efficient for smaller production runs, allowing manufacturers to create custom pieces without high setup costs.
2.3 Water Jet Cutting
Water jet cutting uses a high-pressure stream of water mixed with an abrasive substance to cut aluminum without generating heat.
- Heat-Free Process: Water jet cutting prevents thermal distortion, making it ideal for applications where precise tolerances are critical.
- Suitable for Thick Materials: This method can cut thick aluminum plates, supporting applications in heavy machinery and structural components.
- Environmentally Friendly: Water jet cutting is eco-friendly, as it doesn’t produce hazardous fumes or waste, supporting sustainable fabrication.
2.4 Plasma Cutting
Plasma cutting involves creating an electric arc through a high-velocity jet of ionized gas to cut aluminum.
- High-Speed Cutting: Plasma cutting is a fast and efficient method for cutting aluminum sheets, pipes, and tubes.
- Cost-Effective for Thick Aluminum: Plasma cutting is affordable for thicker materials, making it suitable for industrial applications.
- Rougher Edge Finishes: While plasma cutting is fast, it may leave a rougher edge compared to laser or water jet cutting, often requiring additional finishing.
These cutting techniques enable manufacturers to shape aluminum to exact specifications, supporting diverse applications that require precision, durability, and aesthetic appeal.
3: Joining Techniques in Aluminum Fabrication
Joining methods, such as welding and adhesive bonding, play a crucial role in assembling aluminum components. The choice of technique depends on the strength, durability, and intended use of the final product.
3.1 Welding
Welding is a popular method for joining aluminum components, providing strong, durable bonds.
- TIG Welding (Tungsten Inert Gas): TIG welding is highly precise, ideal for thin aluminum materials where control over heat input is essential.
- MIG Welding (Metal Inert Gas): MIG welding is faster and suited for thicker aluminum parts, commonly used in automotive and construction applications.
- Laser Welding: Laser welding is precise and effective for intricate aluminum components, supporting applications in aerospace, electronics, and high-tech manufacturing.
3.2 Brazing
Brazing involves heating aluminum and a filler material to join components without melting the aluminum itself.
- Suitable for Thin Materials: Brazing is ideal for joining thin aluminum sheets without warping or distortion.
- Smooth, Aesthetic Joints: The process creates visually appealing joints, making it suitable for consumer products and decorative applications.
- Lower Temperature Process: Brazing uses lower temperatures than welding, reducing thermal distortion and preserving material properties.
3.3 Adhesive Bonding
Adhesive bonding involves using specialized adhesives to join aluminum parts, particularly useful in lightweight applications.
- Vibration Damping: Adhesive bonding absorbs vibrations, making it ideal for applications in automotive and electronics where vibration damping is essential.
- Corrosion Resistance: Adhesives provide a protective barrier, enhancing corrosion resistance and extending the lifespan of the joint.
- Lightweight and Flexible: Adhesive bonding is lightweight and adaptable, ideal for applications requiring flexibility without added bulk.
3.4 Mechanical Fastening
Mechanical fastening uses rivets, bolts, and screws to join aluminum components, allowing for easy disassembly and repair.
- Ideal for Modular Designs: Mechanical fasteners support modular assembly, allowing for easy upgrades or repairs.
- Durable and Strong Joints: Fasteners provide reliable connections, especially in heavy-duty applications like aerospace and industrial machinery.
- Reusable and Adjustable: Mechanical fasteners are reusable, supporting flexible assembly and maintenance practices.
Each joining technique has unique advantages, allowing manufacturers to select the best method based on factors such as durability, aesthetics, and flexibility.
4: Forming Techniques in Aluminum Fabrication
Forming techniques allow aluminum to be shaped and molded without removing material, supporting efficient production of custom profiles and complex shapes.
4.1 Extrusion
Extrusion is a form of aluminum fabrication where heated aluminum is pushed through a die to create continuous profiles with specific cross-sectional shapes.
- Custom Profiles for Diverse Applications: Aluminum extrusions support custom designs, ideal for creating parts used in automotive frames, window profiles, and electronic housings.
- High Production Speed: Extrusion is efficient and supports high production rates, making it cost-effective for large-scale manufacturing.
- Precision in Complex Shapes: Extrusion enables the creation of multi-hollow profiles and complex shapes with precision, minimizing the need for secondary machining.
4.2 Rolling
Rolling involves passing aluminum between rollers to reduce thickness and create sheets or coils.
- Efficient Sheet Metal Production: Rolling produces uniform aluminum sheets and coils used in automotive, construction, and packaging.
- Cold Rolling for Precision: Cold rolling creates thin, precise aluminum sheets used in electronics, aerospace, and decorative applications.
- Hot Rolling for High-Volume Production: Hot rolling is used for thick aluminum plates in applications that require durability and structural integrity.
4.3 Forging
Forging involves applying compressive forces to shape aluminum into high-strength components, commonly used in aerospace and heavy machinery.
- Increased Strength: Forging enhances aluminum’s strength, making it ideal for load-bearing applications in industrial machinery and aerospace.
- Precision for High-Stress Applications: Forged aluminum parts provide reliable performance in high-stress conditions, such as aerospace and automotive engines.
- Cost-Effective for High Volume: Forging is efficient for high-volume production, reducing per-unit costs in large-scale manufacturing.
4.4 Casting
Casting involves pouring molten aluminum into a mold to create parts with intricate shapes and complex geometries.
- Ideal for Complex Designs: Casting supports complex, detailed shapes that are challenging to achieve with other methods, ideal for automotive and electronics applications.
- Wide Range of Sizes: Aluminum casting supports a wide range of part sizes, from small electronic components to large machinery housings.
- Cost-Effective for Complex Parts: Casting is a cost-effective option for complex parts, minimizing the need for additional machining.
These forming techniques allow manufacturers to create custom aluminum components efficiently, supporting a wide range of shapes, sizes, and applications.
5: Surface Treatments for Aluminum Fabrication
Surface treatments enhance aluminum’s appearance, durability, and corrosion resistance, supporting applications that require aesthetics and protection.
5.1 Anodizing
Anodizing involves creating a protective oxide layer on aluminum, enhancing durability and corrosion resistance.
- Enhanced Corrosion Protection: Anodizing provides a durable layer that protects aluminum from corrosion, ideal for outdoor and marine applications.
- Aesthetic Finishes: The anodizing process allows for color customization, supporting applications that require aesthetic appeal, such as architectural products.
- Improved Wear Resistance: Anodizing hardens the surface, enhancing wear resistance in high-traffic and high-contact applications.
5.2 Powder Coating
Powder coating involves applying a dry powder to aluminum, which is then cured to form a protective layer.
- Color Versatility: Powder coating offers a wide range of colors, providing decorative options for consumer and architectural applications.
- Increased Durability: Powder-coated surfaces resist impacts, abrasions, and chemicals, extending the lifespan of aluminum products.
- Eco-Friendly Process: Powder coating is environmentally friendly, as it produces minimal waste and avoids solvents used in traditional paint..
5.3 Electroplating
Electroplating deposits a thin layer of metal onto aluminum, enhancing appearance and corrosion resistance.
- Enhanced Durability and Hardness: Electroplating provides a hard, durable finish that resists wear, ideal for high-contact applications.
- Improved Corrosion Protection: Electroplating adds a protective barrier, preventing corrosion and extending component life.
- Metallic Finishes: Electroplating offers metallic finishes like chrome or nickel, creating aesthetic and functional layers for various applications.
These surface treatments allow manufacturers to enhance aluminum’s properties, making it suitable for both functional and decorative purposes.
Conclusion: Aluminum Fabrication Techniques for Modern Manufacturing
Aluminum fabrication techniques provide manufacturers with the flexibility, precision, and durability required to meet the demands of modern manufacturing. From cutting and joining to forming and finishing, each technique supports the creation of high-quality aluminum components that are lightweight, strong, and sustainable.
With advancements in technology, aluminum fabrication continues to evolve, supporting industries that require efficient, eco-friendly, and cost-effective solutions. Whether it’s for aerospace, automotive, construction, or electronics, aluminum’s versatility ensures that it remains a critical material in shaping the future of manufacturing.