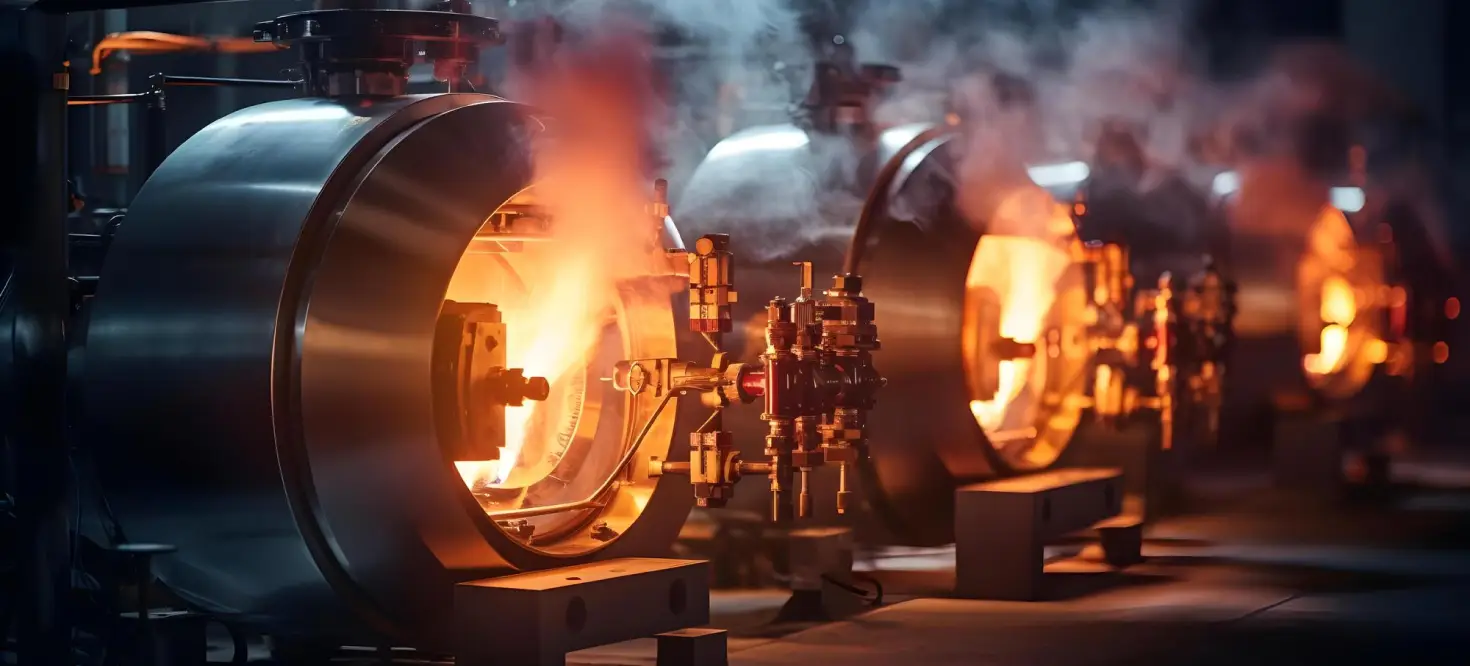
Sep 10 2024
/
How Billet Casting is Transforming Aluminum Manufacturing Efficiency
In the rapidly evolving world of manufacturing, billet casting has emerged as a game-changer in the aluminum industry, fundamentally transforming how we approach production, sustainability, and efficiency. As industries look for lighter, stronger, and more versatile materials, aluminum has consistently been a favorite due to its unique properties. Billet casting takes this a step further by enhancing the efficiency and sustainability of aluminum manufacturing processes. In this blog post, we’ll dive deep into billet casting, its impact on aluminum production, and how companies like National Industries are pioneering innovations in this field.
What is Billet Casting?
Billet casting is the process of creating semi-finished aluminum blocks, known as billets, which can be further processed into a variety of products such as extrusions, rolled products, or forged components. Aluminum billets are typically produced through a continuous casting process, where molten aluminum is poured into a mold and then cooled. Once cooled, these billets can be re-heated and used in extrusion processes to create custom aluminum profiles.
This process is integral to industries like automotive, aerospace, construction, and many others where aluminum components are essential. By utilizing billet casting, manufacturers can significantly improve the efficiency of aluminum production, ensuring consistency in material quality, reducing waste, and optimizing energy consumption.
The Role of Billet Casting in Enhancing Efficiency
- Improved Material Utilization
One of the key ways billet casting boosts manufacturing efficiency is through improved material utilization. Traditional manufacturing methods often lead to significant waste, but billet casting minimizes this by creating near-net shapes that reduce the need for extensive machining. This means manufacturers can use more of the raw material in the final product, cutting down on waste and optimizing resource use. - Energy Efficiency
In aluminum manufacturing, energy costs can be substantial. Billet casting significantly reduces the energy required by using continuous casting processes that optimize the solidification of molten aluminum. By producing billets directly from the molten metal in a continuous process, there’s less need for re-melting and re-heating, leading to considerable energy savings. The energy-efficient nature of billet casting is especially crucial in industries focused on sustainability and reducing their carbon footprint. - Consistency in Quality
In any manufacturing process, consistency in material quality is critical. Billet casting allows for greater control over the composition and grain structure of the aluminum, resulting in superior mechanical properties. This ensures that manufacturers receive high-quality aluminum billets that meet stringent specifications, improving the overall reliability of their products.
For companies like National Industries, this level of control is essential in delivering high-quality aluminum solutions to clients across diverse sectors like defense, aerospace, and industrial machinery. Consistency in material quality leads to fewer defects, less rework, and ultimately, higher production efficiency.
How Billet Casting Aligns with Modern Manufacturing Needs
- Sustainability and Waste Reduction
Sustainability is no longer a buzzword in manufacturing—it’s a necessity. With global pressures to reduce emissions and minimize environmental impacts, manufacturers are constantly seeking processes that allow them to meet these goals without sacrificing efficiency. Billet casting is a prime example of a manufacturing process that aligns with sustainability objectives.
Traditional aluminum manufacturing methods generate a lot of scrap material, but billet casting significantly reduces this by optimizing the shape and size of the billet according to the specific needs of the extrusion process. This means less material waste, and more efficient use of aluminum, which is already one of the most recyclable materials available. Companies like National Industries are at the forefront of leveraging billet casting to meet both efficiency and environmental goals. - Customization and Flexibility
In today’s fast-paced industrial environment, manufacturers require flexible and customizable solutions to meet their clients’ unique demands. Billet casting allows for a high degree of customization in terms of alloy composition, billet size, and shape. This flexibility enables manufacturers to quickly adapt to changes in market demands or specific customer requirements, all while maintaining high production efficiency.
National Industries’ ability to cast billets in a wide range of sizes and compositions is a key advantage, especially as they expand their extrusion capabilities to produce larger and more complex aluminum profiles. The company’s state-of-the-art extrusion press, capable of handling up to 8600 metric tons, is a testament to how billet casting can support scalable and flexible manufacturing processes.
Impact of Billet Casting on Various Industries
Billet casting has wide-reaching applications across many sectors that rely heavily on aluminum for its lightweight and durable properties. Let’s explore how this process is transforming a few key industries:
- Automotive Industry
In the automotive sector, manufacturers are continuously seeking ways to reduce vehicle weight to improve fuel efficiency and reduce emissions. Aluminum plays a critical role in this, and billet casting enables the production of high-quality, lightweight components at a lower cost. For instance, aluminum extrusions made from billets can be used in chassis, body panels, and other structural parts, contributing to overall vehicle efficiency. - Aerospace and Defense
Aerospace and defense industries demand high-strength materials that can withstand extreme conditions while being lightweight enough to ensure fuel efficiency and agility. Billet casting produces aluminum components with uniform grain structure, resulting in higher strength-to-weight ratios. This makes billet-cast aluminum ideal for aircraft frames, military vehicles, and weapon systems.
National Industries is proud to support these industries by offering billet-cast aluminum solutions that meet stringent regulatory standards and offer unparalleled performance in critical applications. - Construction and Infrastructure
As urbanization continues to accelerate, the construction industry is increasingly reliant on aluminum for its corrosion resistance, lightweight properties, and structural strength. Billet casting allows manufacturers to produce durable extruded aluminum profiles that are used in everything from skyscrapers to bridges. These profiles are essential in creating long-lasting infrastructure that is both energy-efficient and cost-effective.
How National Industries is Leading the Way in Billet Casting
As one of India’s leading aluminum extrusion manufacturers, National Industries is at the forefront of billet casting technology. The company has invested in advanced billet casting facilities that enable them to produce high-quality aluminum billets that meet the needs of a wide range of industries.
National Industries’ commitment to technological advancement is evident in its recent introduction of India’s largest extrusion press, capable of producing both solid and hollow profiles with remarkable precision. This new capability allows the company to offer larger, more complex profiles that can’t be manufactured through traditional methods, making it a leader in the aluminum extrusion industry.
By using billet casting, National Industries can ensure that their aluminum products are of the highest quality, with excellent mechanical properties and minimal waste. This enables the company to serve clients in industries ranging from automotive to aerospace with precision-engineered aluminum solutions that drive efficiency and innovation.
The Future of Billet Casting in Aluminum Manufacturing
As industries continue to prioritize sustainability, efficiency, and innovation, billet casting will play an even more vital role in the aluminum manufacturing landscape. The ability to produce high-quality aluminum billets with reduced energy consumption, waste, and production time makes billet casting a cornerstone of modern manufacturing.
At National Industries, we recognize the importance of staying ahead of technological trends, which is why we continue to invest in cutting-edge billet casting and extrusion technologies. Our goal is to provide our clients with the best possible aluminum solutions, whether it’s for automotive components, construction projects, or aerospace applications.
In the future, advancements in billet casting will likely lead to even more efficient production processes, further reducing costs and environmental impact. Companies that embrace these innovations will be better positioned to meet the growing demand for lightweight, durable, and sustainable materials.
Conclusion
Billet casting is revolutionizing the aluminum manufacturing industry by offering a more efficient, sustainable, and customizable solution for producing high-quality aluminum components. With its ability to reduce waste, enhance material utilization, and improve energy efficiency, billet casting is transforming how manufacturers approach production.
As a leader in this field, National Industries is committed to leveraging billet casting to deliver top-tier aluminum solutions that meet the evolving needs of industries worldwide. By continuing to innovate and invest in state-of-the-art technology, National Industries is helping to shape the future of aluminum manufacturing for years to come. If you’re looking for high-quality, customized aluminum extrusion solutions, contact National Industries today and discover how billet casting can transform your manufacturing processes.