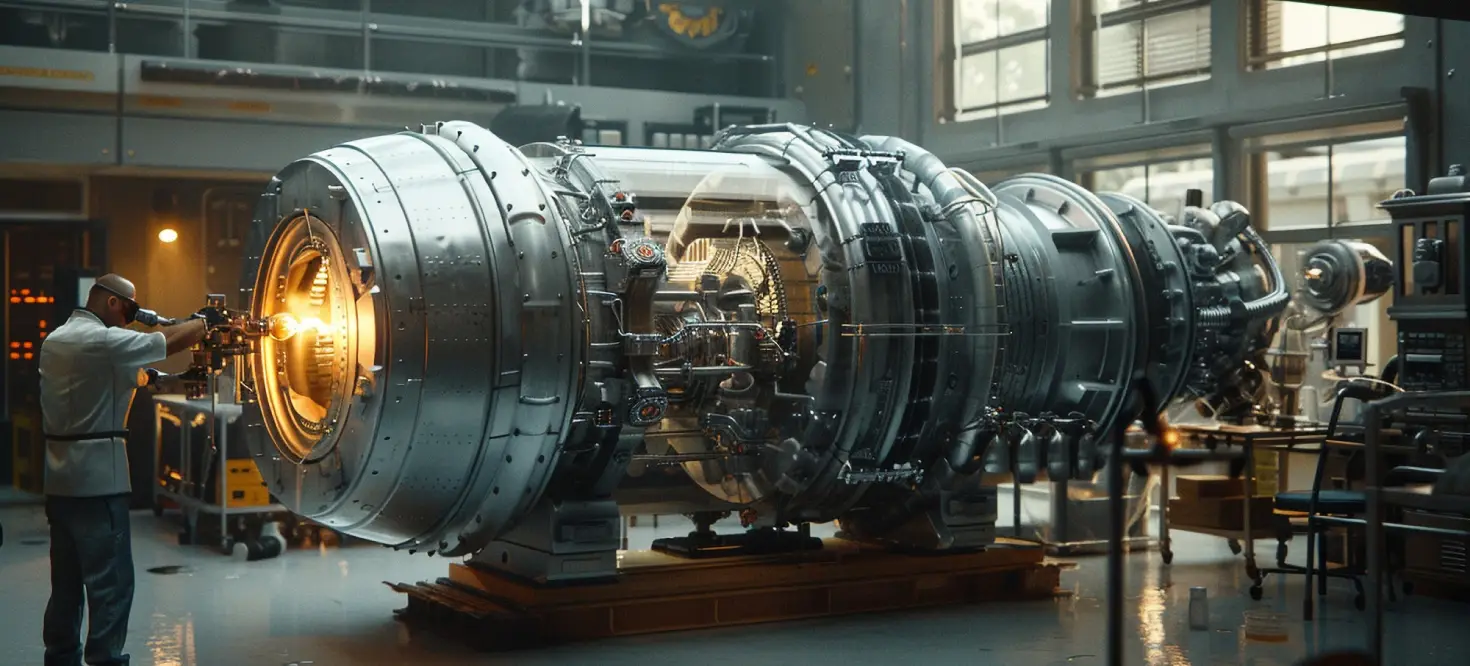
Sep 10 2024
/
The Science Behind Alloy Development: How New Compositions are Shaping Industries
Introduction
In today’s rapidly evolving industrial landscape, the demand for advanced materials is stronger than ever. At the heart of this transformation is alloy development, a field where science and innovation converge to create new compositions that enhance material properties and unlock new possibilities across various industries. From aerospace to automotive, and electronics to construction, alloys play a critical role in shaping the future of technology and manufacturing. As a leader in the aluminum industry, National Industries continues to pioneer advancements in alloy development, delivering tailored solutions that meet the specific needs of a diverse range of sectors.
This blog delves into the science behind alloy development and explores how new compositions are reshaping industries. We will examine the critical processes involved, highlight recent innovations, and discuss the future trends driving alloy technology forward.
Understanding Alloys: A Foundation of Modern Industry
An alloy is a mixture of two or more elements, where at least one of the elements is a metal. The purpose of alloying is to enhance specific material properties, such as strength, corrosion resistance, ductility, and thermal stability. By combining different elements, alloy developers can create materials that outperform pure metals in various applications.
For instance, pure aluminum, while lightweight and corrosion-resistant, lacks the mechanical strength required for many industrial applications. However, when alloyed with elements like magnesium, silicon, copper, and zinc, aluminum’s strength and hardness improve significantly, making it suitable for everything from aircraft frames to automotive components.
Key Properties of Alloys
- Strength and Durability: Alloying enhances the tensile and yield strength of metals, making them more suitable for heavy-duty applications.
- Corrosion Resistance: Certain alloys offer improved resistance to oxidation and corrosion, extending the lifespan of materials used in harsh environments.
- Weight: By combining metals like aluminum and titanium, lightweight yet strong alloys are created, which are crucial for sectors like aerospace and transportation.
- Thermal and Electrical Conductivity: Alloying can also improve a material’s ability to conduct heat or electricity, making it more efficient for electrical or heat-dissipating components.
The Science of Alloy Development
Alloy development is a highly scientific process, combining materials science, chemistry, and engineering to manipulate the properties of base metals. The process typically involves three key stages:
- Alloy Design: This is the initial phase where developers select the base metal and alloying elements. The choice of elements depends on the desired material properties. For example, adding copper to aluminum improves its strength, while magnesium enhances its ductility. Modern alloy design often leverages computational models and simulations to predict how different compositions will behave under various conditions.
- Manufacturing Processes: Once an alloy composition is determined, the next step is the actual production. This involves melting and mixing the base metal with alloying elements in precise proportions. Advanced techniques such as billet casting and powder metallurgy play a significant role here. National Industries, for example, utilizes state-of-the-art extrusion technology to produce high-quality aluminum alloys for a range of industrial applications.
- Testing and Optimization: After production, alloys undergo rigorous testing to ensure they meet performance requirements. This may involve mechanical testing (such as tensile strength tests) and environmental testing (such as corrosion resistance in saltwater environments). Data collected from these tests allows developers to fine-tune the alloy composition for maximum performance.
Alloying Elements: A Breakdown of Common Additives
Each element added to an alloy serves a unique purpose. Understanding the role of these elements is crucial in appreciating the science behind alloy development.
- Aluminum (Al): Lightweight, corrosion-resistant, and highly malleable, aluminum serves as a base for many modern alloys, especially in industries like aerospace, automotive, and construction.
- Magnesium (Mg): Adds strength and improves the machinability of alloys while maintaining light weight, making it an ideal additive for structural applications.
- Copper (Cu): Enhances electrical conductivity and mechanical strength but can reduce corrosion resistance in certain environments.
- Zinc (Zn): Often used in combination with aluminum, zinc increases strength and hardness, making it popular in industries like construction and automotive.
- Silicon (Si): Improves the castability of alloys and reduces their weight, while also contributing to corrosion resistance.
- Titanium (Ti): Known for its exceptional strength-to-weight ratio, titanium is used in high-performance applications such as aerospace and biomedical devices.
New Compositions in Alloy Development: A Game Changer
Innovation in alloy development has led to the creation of new compositions that address industry-specific challenges. As industries push the boundaries of performance, developers are exploring novel alloys that offer unique benefits. Some of the most significant breakthroughs include:
- High-Strength Aluminum Alloys: With the global shift towards lightweighting, high-strength aluminum alloys are gaining prominence. These alloys, designed for maximum strength-to-weight ratio, are being increasingly adopted in the automotive and aerospace sectors. By reducing vehicle weight, these alloys help improve fuel efficiency and reduce carbon emissions.
- Corrosion-Resistant Superalloys: In industries such as oil and gas and marine engineering, materials must withstand extreme conditions, including high temperatures, pressure, and corrosive environments. Superalloys, often composed of nickel, cobalt, and chromium, offer unparalleled resistance to degradation. Their use in turbine blades, exhaust systems, and other critical components has proven transformative in extending the lifespan of industrial equipment.
- High-Entropy Alloys (HEAs): A revolutionary class of materials, high-entropy alloys are composed of five or more elements in roughly equal proportions. Unlike traditional alloys, which typically rely on one dominant base metal, HEAs exhibit unique combinations of properties such as superior strength, ductility, and resistance to wear and corrosion. HEAs are opening new frontiers in defense, aerospace, and energy storage applications.
Industrial Applications: Shaping the Future
The development of new alloy compositions is directly tied to the needs of various industries. As requirements for lighter, stronger, and more sustainable materials increase, alloy developers are rising to the challenge. Here’s a look at some industries that are being shaped by advancements in alloy technology:
- Aerospace: Aerospace demands materials that are not only lightweight but also capable of withstanding extreme stress and temperature fluctuations. Advanced aluminum-lithium alloys, for instance, are widely used in aircraft frames due to their lightweight properties and superior fatigue resistance.
- Automotive: In the automotive industry, alloy development is essential for reducing vehicle weight without compromising safety or performance. Aluminum-magnesium alloys are frequently used in structural components, while high-strength steels are employed in safety-critical parts such as bumpers and crash beams.
- Renewable Energy: As the world transitions towards renewable energy, materials capable of handling the unique stresses in solar panels, wind turbines, and energy storage systems are critical. Alloy advancements have enabled the production of materials with enhanced durability and efficiency, ensuring longer lifespans and lower maintenance costs for renewable energy infrastructure.
- Construction: The construction industry continues to benefit from the development of corrosion-resistant and lightweight alloys. Modern buildings and bridges, particularly in coastal or industrial areas, utilize advanced aluminum-zinc alloys that offer long-term durability without the need for constant maintenance.
National Industries’ Role in Alloy Development
National Industries has always been at the forefront of alloy innovation. With its cutting-edge extrusion technology and commitment to research and development, National Industries has played a pivotal role in transforming the aluminum alloy landscape. By collaborating with industry leaders and leveraging state-of-the-art technologies, National Industries provides customized alloy solutions that cater to the unique demands of the transportation, renewable energy, defense, and construction sectors.
As the demand for lightweight, strong, and sustainable materials grows, National Industries continues to lead the way in alloy development, offering innovative products that drive efficiency and performance across multiple industries.
Future Trends in Alloy Development
Looking forward, several trends are expected to shape the future of alloy development:
- Sustainability: As environmental regulations tighten, the demand for recyclable and eco-friendly alloys will rise. Alloy developers are focusing on creating materials with lower carbon footprints while maintaining high performance.
- 3D Printing and Additive Manufacturing: The rise of additive manufacturing is revolutionizing alloy development. This technology enables the creation of custom alloys that can be precisely tailored to specific applications, opening new possibilities in fields such as biomedical devices and aerospace engineering.
- Nanotechnology: The use of nanotechnology in alloy development is unlocking new material properties, such as increased hardness, thermal conductivity, and corrosion resistance, enabling breakthroughs in industries like electronics and defense.
Conclusion
The science behind alloy development is driving profound changes across multiple industries, enabling manufacturers to push the boundaries of what’s possible with materials. As new compositions emerge, industries ranging from aerospace to renewable energy are benefiting from lighter, stronger, and more efficient materials.
National Industries continues to be at the forefront of alloy innovation, delivering custom alloy solutions that meet the evolving needs of today’s industrial landscape. Through its commitment to research, quality, and sustainability, National Industries is shaping the future of alloy development and driving technological advancement across industries.
For more information on alloy development and its applications, visit National Industries.