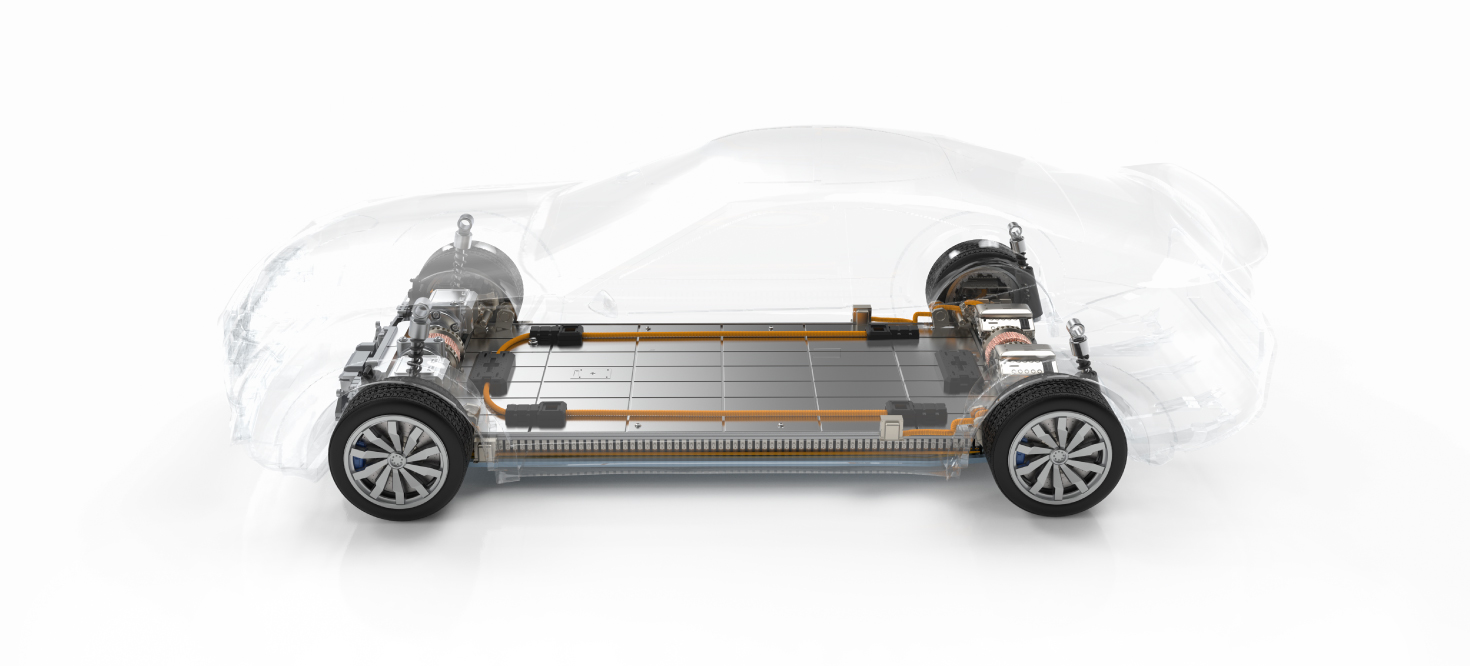
Mar 21 2025
/
Precision and Strength: Meeting the Demands of the Electronics Industry
Introduction
As technology advances, the electronics industry faces increasing demands for high precision, durability, and heat management. With devices becoming smaller, faster, and more complex, the need for precision-engineered materials that provide both strength and functionality is essential. Materials like aluminum, known for its strength-to-weight ratio, thermal conductivity, and corrosion resistance, play a vital role in electronics. From heat sinks and casings to connectors and circuit boards, aluminum and other strong materials enable manufacturers to produce devices that meet the high-performance standards of modern electronics.
This blog explores the role of precision and strength in electronics manufacturing, examining how materials like aluminum support innovations in miniaturization, durability, and thermal management. By understanding the importance of these materials, we can appreciate how the industry meets the complex demands of today’s technology-driven world.
1: Why Precision and Strength Are Essential in the Electronics Industry
1.1 High-Performance and Durability
As consumer expectations rise, electronic devices need to be durable and high-performing to support complex functions in a variety of environments.
Protection in Harsh Environments: Durable materials like aluminum provide protection against elements such as moisture, dust, and temperature changes, which is essential for outdoor and industrial applications.
- Longevity and Reliability: Durable materials prevent wear and tear, ensuring that devices like smartphones, laptops, and industrial electronics have long service lives.
- Increased Device Lifespan: High-strength materials allow components to withstand physical stresses, reducing the need for frequent repairs and replacements.
- Protection in Harsh Environments: Durable materials like aluminum provide protection against elements such as moisture, dust, and temperature changes, which is essential for outdoor and industrial applications.
1.2 Precision in Miniaturized Components
Miniaturization has become a trend in electronics, requiring components to be smaller and more complex while maintaining precision.
- Optimized Space Utilization: Precision manufacturing allows for smaller components that optimize space, enabling more compact and powerful devices.
- High Accuracy for Complex Functions: Precision engineering ensures that components perform accurately, essential for high-tech functions in devices like medical equipment and aerospace electronics.
- Alignment with Consumer Expectations: As devices become more compact, precision is necessary to meet the expectations of consumers for high-quality, feature-rich electronics.
1.3 Heat Management and Efficiency
Electronics generate heat during operation, making effective thermal management critical to prevent overheating and maintain performance.
- Enhanced Thermal Conductivity: Materials like aluminum are excellent heat conductors, dispersing heat quickly and efficiently to maintain device functionality.
- Protection Against Overheating: Effective heat dissipation prevents overheating, which can damage sensitive electronic components and reduce their lifespan.
- Energy Efficiency: Improved thermal management helps devices operate more efficiently, reducing energy consumption and supporting sustainability goals.
These factors highlight why precision and strength are essential in the electronics industry, supporting durability, miniaturization, and thermal management for reliable, high-performing devices.
2: Key Applications of Precision and Strength in Electronic Components
Materials that offer both precision and strength are essential in various electronic applications, providing durability, functionality, and efficiency across devices.
2.1 Heat Sinks for Thermal Management
Heat sinks are crucial components in electronics, using materials like aluminum to disperse heat and keep devices cool.
- High Thermal Conductivity: Aluminum heat sinks absorb and dissipate heat from components like CPUs, GPUs, and power transistors, protecting against overheating.
- Precision Design for Effective Cooling: Heat sinks are designed with precision fins and channels to maximize surface area and improve airflow, enhancing cooling efficiency.
- Lightweight for Space Efficiency: Aluminum’s lightweight nature allows for compact heat sinks that don’t add significant bulk, ideal for compact devices and portable electronics.
2.2 Durable Casings and Enclosures
Casings made of strong, lightweight materials protect internal components from physical damage and environmental factors.
- Impact-Resistant Aluminum Casings: Aluminum’s strength protects against impacts, drops, and scratches, ensuring that devices remain functional despite daily wear.
- Corrosion Resistance for Outdoor Applications: Aluminum is corrosion-resistant, making it ideal for enclosures used in outdoor or industrial settings.
- Precision in Design for Seamless Integration: Precision-engineered aluminum casings provide a snug fit for internal components, supporting aesthetic design and ease of assembly.
2.3 Connectors and Circuit Board Frames
Connectors and frames support the structural integrity and alignment of circuit boards, essential for reliable electronic performance.
- Precision Machining for Accurate Alignment: High-precision machining ensures connectors and frames align perfectly, preventing circuit interruptions and improving signal stability.
- Strength for Structural Support: Durable materials provide stability to circuit boards, preventing bending or breaking that could cause device malfunction.
- Corrosion Resistance for Reliability: Corrosion-resistant materials protect circuit boards from environmental damage, essential for industrial and automotive electronics.
2.4 Battery Casings and Thermal Management Systems
Battery casings require materials that provide protection and heat dissipation, supporting the safety and efficiency of devices.
- Lightweight Aluminum Battery Enclosures: Aluminum casings protect batteries from physical damage without adding significant weight, ideal for mobile devices and electric vehicles.
- Heat Dissipation for Battery Safety: Aluminum’s thermal conductivity supports heat dissipation, preventing overheating and enhancing battery life.
- Customized Designs for Battery Modules: Precision manufacturing allows for customized battery casing designs that optimize space and performance, supporting compact and powerful energy solutions.
These applications demonstrate how precision and strength are vital to electronics, supporting durability, functionality, and thermal efficiency across various device types.
3: Advantages of Aluminum in Electronics for Precision and Strength
Aluminum is widely used in electronics due to its unique properties that meet the industry’s demands for precision, strength, and durability.
3.1 High Strength-to-Weight Ratio
Aluminum’s strength-to-weight ratio makes it ideal for electronics where durability and portability are essential.
- Lightweight for Portable Devices: Aluminum provides strength without added bulk, supporting lightweight and portable device designs, such as smartphones and laptops.
- Structural Integrity Without Excess Weight: High-strength aluminum provides structural support in devices, reducing the risk of damage without adding unnecessary weight.
- Support for Wearable Electronics: Lightweight aluminum components are used in wearables, offering durability and comfort for devices like fitness trackers and smartwatches.
3.2 Excellent Thermal Conductivity for Effective Heat Management
Aluminum’s high thermal conductivity makes it ideal for heat dissipation in electronic components that generate significant heat.
- Efficient Heat Dissipation in Compact Designs: Aluminum heat sinks prevent overheating by dispersing heat quickly, especially important for compact devices with limited airflow.
- Extended Lifespan of Components: By managing heat effectively, aluminum helps extend the lifespan of sensitive components, reducing the risk of failure due to thermal stress.
- Support for High-Performance Applications: Aluminum’s thermal properties are essential for high-performance devices, such as gaming consoles, that require efficient cooling.
3.3 Corrosion Resistance for Long-Lasting Performance
Aluminum’s natural resistance to corrosion makes it suitable for outdoor and industrial electronics, which are often exposed to harsh environments.
- Protection Against Moisture and Humidity: Aluminum resists moisture and humidity, preventing damage and supporting reliable operation in diverse climates.
- Durability in High-Exposure Settings: Corrosion-resistant aluminum enclosures protect devices used in industrial, automotive, and outdoor applications, extending their service life.
- Low Maintenance Requirements: Aluminum’s corrosion resistance reduces maintenance needs, making it cost-effective for long-term use in electronics.
3.4 Recyclability and Sustainability
Aluminum’s recyclability aligns with sustainable manufacturing goals, supporting the electronics industry’s focus on eco-friendly practices.
- Energy Savings from Recycled Aluminum: Using recycled aluminum reduces energy consumption, lowering the environmental impact of electronics production.
- Alignment with Green Initiatives: Recyclable materials like aluminum help electronics manufacturers meet sustainability goals and reduce waste.
- Circular Economy Compatibility: Aluminum’s recyclability supports a circular economy, making it a responsible choice for electronic products with environmental considerations.
These benefits make aluminum indispensable in electronics, providing the precision and strength necessary for modern devices while supporting sustainability.
4: Technological Advancements in Precision and Strength for Electronics
Advances in material technology and precision engineering are expanding the capabilities of aluminum and other materials in electronics, supporting innovation in miniaturization, durability, and functionality.
4.1 Precision Extrusion for Complex and Miniaturized Components
Modern extrusion techniques enable the creation of highly precise aluminum components that meet the demands of compact and intricate electronics.
- Multi-Hollow Profiles for Lightweight Strength: Multi-hollow aluminum profiles provide strength without added weight, ideal for frames and support structures in electronics.
- Custom Designs for Heat Sinks and Connectors: Precision extrusion allows for detailed profiles, enhancing thermal performance and connectivity.
- Reduced Waste in Production: Precision extrusion reduces waste, supporting sustainable manufacturing by using only the necessary material.
4.2 Surface Treatments for Enhanced Durability and Appearance
Surface treatments improve corrosion resistance, scratch resistance, and aesthetics, supporting aluminum’s long-term performance in electronics.
- Anodizing for Enhanced Corrosion Protection: Anodized aluminum offers extra corrosion resistance and a sleek finish, ideal for consumer electronics casings.
- Powder Coating for Scratch Resistance: Powder coating adds a layer of protection against scratches, preserving the appearance of aluminum in high-touch areas.
- Anti-Reflective Coatings for Display Components: Specialized coatings reduce glare and improve visibility on screens, enhancing user experience in devices like smartphones and tablets.
4.3 Hybrid Materials and Aluminum Alloys for High Performance
Hybrid materials and advanced aluminum alloys provide enhanced strength, heat resistance, and durability, meeting the specific needs of high-performance electronics.
- Aluminum-Carbon Fiber Hybrids for Lightweight Strength: Combining aluminum with carbon fiber produces a lightweight, high-strength material ideal for structural support in compact electronics.
- Aluminum Alloys for Enhanced Thermal Management: Advanced alloys provide improved thermal conductivity, supporting high-performance applications like gaming consoles and data centers.
- Hybrid Battery Enclosures for EVs and Portable Devices: Hybrid materials support battery enclosures that optimize thermal management and impact resistance, essential for electric vehicles and mobile electronics.
These technological advancements are expanding aluminum’s applications in electronics, enabling manufacturers to create devices that are durable, efficient, and sustainable.
Conclusion: The Role of Precision and Strength in Modern Electronics
As electronic devices become more compact, powerful, and complex, the need for materials that offer precision and strength is more important than ever. Aluminum’s unique combination of durability, thermal conductivity, and corrosion resistance makes it an invaluable material in the electronics industry. From heat sinks and casings to connectors and battery enclosures, aluminum supports the high-performance demands of modern electronics, enhancing device longevity and user experience.
With advancements in extrusion, surface treatments, and hybrid materials, aluminum continues to meet the evolving needs of the electronics industry, supporting innovation in both design and functionality. By investing in precision and strength, the electronics industry can develop smarter, more efficient devices that align with the demands of today’s technology-driven world, while also promoting sustainability.